CNC Precision Machining
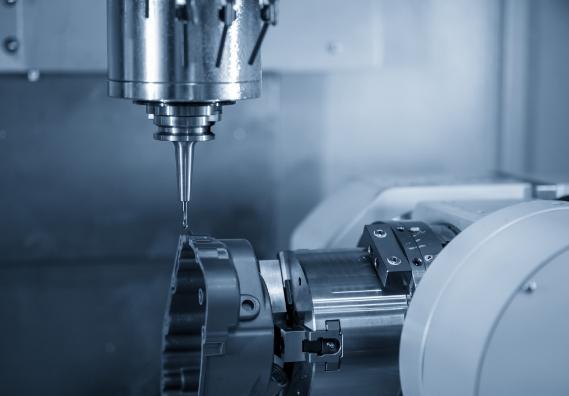
Feng Ching Enterprise can design the optimal milling methods and processes based on the complexity of the machined parts, budget considerations, and specific requirements, we design the optimal milling methods and processes to achieve the desired results, with a tolerance of +/-0.01mm.
Currently, we own and operate 60 machines, providing customers with high-precision and high-efficiency manufacturing services on a daily basis. Product quality is ensured through professional inspection procedures, such as 3D Coordinate-measuring machines.
Precision CNC Machining Shop
In conclusion, our CNC machining services offer a range of capabilities from 3-axis to 5-axis milling machines, allowing us to meet various customer needs for precision, complexity, and efficiency in metal machining.
The Process of CNC machining
CNC machining technology plays a crucial role in modern industrial production, enabling the automation of manufacturing processes. In the process of creating a product from scratch, CNC machining generally involves the following steps:
Design CAD drawings |
Firstly, use computer-aided design software to create the required
product drawings.
|
Programming
|
Programming - Based on the drawing design, use CAM software to write CNC
programs, which consist of instruction sets including processing path, cutting
speed, feed speed and other parameters.
|
Processing preparation
|
Place the raw material on the CNC machine, fix and adjust its position, and equip the cutting tool on the machine. |
Start processing
|
Input the machining program into the CNC machine controller, and the machine can automatically process according to the predetermined path. |
Quality inspection
|
After processing is completed, it is necessary to inspect whether the
product’s dimensions, surface roughness and shape meet the requirements before
proceeding to the subsequent process.
|
3-axis CNC milling machine
One of the most common and traditional milling techniques, where the workpiece is fixed on the worktable, and the rotating cutter performs cutting in three linear feed axes:
- X-axis for horizontal movement of the worktable
- Y-axis for vertical movement of the worktable
- Z-axis for vertical movement of the cutter in a direction perpendicular to the worktable
As only three axes are used for cutting, this method is more suitable for parts with regular and simple shapes.
4-axis CNC milling machine
A modification of the original 3-axis machining center, with the addition of a CNC rotary table as the fourth axis, known as the A-axis. This allows the workpiece to be indexed and machined at various angles, enabling complex operations including drilling, milling, circular cutting, and contouring at different angular positions on the machine. This method is suitable for parts that require features such as slanted surfaces, angled holes, threads, or three-dimensional patterns.
Utilizing 4-axis milling can result in improved precision, processing speed, and reduced number of required processes.
5-axis CNC milling machine
A CNC machine tool with 5 degrees of freedom, including X, Y, Z linear axes, and A, B rotational axes.
It is one of the most suitable methods for machining freeform or complex surfaces. This allows the milling cutter to move in five axes simultaneously, enabling complex and precise machining of parts with curved surfaces, undercuts, or intricate geometries.
With the increasing demand in various industries for high-precision manufacturing of complex geometric shapes, such as turbine blades, aerospace components, military parts, etc., the flexibility and precision of multi-axis machining is becoming a trend in the future.