Surface Treatment
We offer customized surface treatment services, tailored to the specific needs of our customers. Surface treatment is a post-machining step, aiming to enhance the appearance, performance, and durability of metal components. Considering that most material damage typically starts from the surface, this technique holds paramount importance in the manufacturing process.
Surface treatment is a process carried out after machining to improve the appearance, performance and durability of metal parts’ surfaces. Since most material damage starts from the surface, surface treatment technology is an important part of the manufacturing process.
Surface treatment can modify the surface characteristics of objects, including aesthetics (gloss, color, roughness), protection (corrosion resistance, extended lifespan), special surface properties (conductivity, weldability), and mechanical properties (enhanced hardness, wear resistance, heat resistance). Before post-processing surface treatment, it is necessary to choose an appropriate surface treatment method according to the material of the workpiece to meet the specific application requirements of the product.
Surface treatment technology is widely used in various industries, including automotive, aerospace, aviation, construction, appliances, machinery, electronics, and more. Common metal surface treatment methods such as grinding, sandblasting, coating, anodizing, and others.
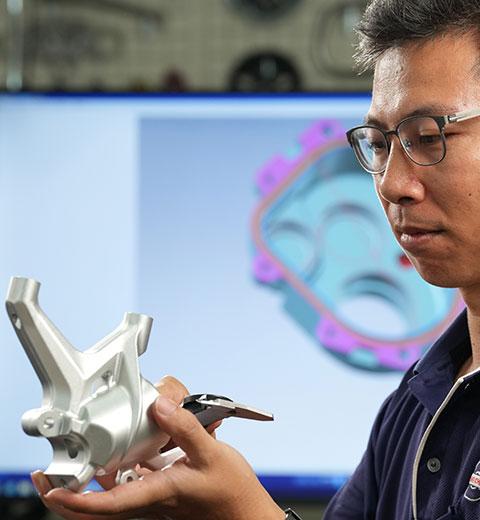
Electroplating
Electroplating is a surface treatment method that uses electrodeposition to form a thin film coating onto a metal surface, aiming to enhance corrosion resistance and aesthetics. Different effects can be achieved depending on the type of coating material used. Examples are as follows:
Utilizing CNC machines to process titanium enables the production of parts with high precision and complex shapes. However, working with titanium requires the use of cutting tools with high hardness and wear resistance. It is also necessary to employ lower cutting speeds and larger feed rates to avoid issues such as thermal deformation of the workpiece and damage to cutting tools.
- Zinc plating: Increases the aesthetic appeal of the metal surface and prevents rusting.
- Chrome plating: Increases the durability, surface brightness, and aesthetic appeal of metal products.
- Gold plating: Used for decoration, preventing oxidation of objects, and has low electrical resistance, ease of soldering, and corrosion resistance.
- Titanium plating: Prevents pollution, reduces the likelihood of allergic reactions when in contact with the human body, and resists acid, alkalis and oxidation.
- Nickel plating: Deposited on metal surface through oxidation-reduction reactions, it enhances corrosion resistance, wear resistance, and adds visual appeal and luster.
Printing
Printing is a process of duplicating patterns, text or images onto products. Screen printing, inkjet printing, and pad printing are common methods used on metal parts:
- Screen printing: It is a widely used metal printing method where ink is applied to the metal surface to transfer patterns using pressure from a squeegee through a meshed printing plate.
- Inkjet printing: A digital printing technique that sprays ink onto the metal surface to create patterns and text. It can achieve high resolution and colorful printing effects.
- Pad printing: The pattern is transferred from a flexible silicone pad onto the metal surface. Pad printing is suitable for printing on parts with irregular shapes, curved surfaces or small areas.
Different printing methods can provide different printing and decorative effects for metal products. The choice of printing method depends on the characteristics of the metal material, desired printing effects, and decorative requirements.
Grinding
Grinding can be divided into manual grinding and machine grinding. Manual grinding uses tools such as sandpaper, abrasive cloth, grinding stones, and metal brushes to manually grind, polish, and refine the metal surface. It offers a high degree of flexibility and control for small batches or custom products.
Machine grinding utilizes mechanical grinding methods to remove surface defects and improve the smoothness, precision, and surface roughness of metal parts. Common grinding tools and equipment such as grinders, grinding wheels, and grinding stones are used to remove defects or unevenness from the surface of workpieces by cutting and rubbing between the tools and the workpiece surface. It is suitable for mass production, high efficiency, and achieving a high level of consistency in products.
Anodizing
Anodizing is an electrochemical method that produces an oxide layer on the surface of metals to improve corrosion resistance, hardness, and at the same time, it can produce a variety of colors and enhance aesthetics. Anodizing is commonly applied to aluminum and other alloys. The process involves placing the metal part in an electrolytic bath and applying a certain voltage and current to form a thick and durable oxide film on the metal surface.The main advantages of anodizing are enhancing the corrosion resistance of the metal to protect it from chemical substances or humid environments. Additionally, the oxide film increases the surface hardness of the workpiece, making it more wear-resistance. Therefore, anodizing is widely used in various industries, including aerospace, automotive, construction, and industrial fields.
Laser engraving
Laser engraving is a machining technique that uses a high-energy laser beam to engrave specific patterns, text, or designs on the surface of an object. It is a non-contact method commonly applied to materials such as metal, plastic, wood, glass and stone.
Painting
Painting is a type of surface treatment where a coating or layer of paint is applied to the surface of an object and then rapidly hardened by heat. It is a common surface finishing method used in a wide range of industries, including automotive manufacturing, furniture production, metal fabrication, electronics and industrial equipment. Painting offers excellent rust resistance, good adhesion, and uniform surface coverage, providing parts with qualities such as durability, corrosion resistance, aesthetics, and wear resistance.
Sandblasting
Also known as abrasive blasting, sandblasting is a process of using high-pressure airflow or compressed gas to propel sand or other abrasives onto the surface of a workpiece at high speed. It is employed to remove surface dirt, oxides, paint and other defects from the object to achieve a smoother finish and prepare for subsequent coating or anodizing processes.