Metal & Alloy Raw Material Processing
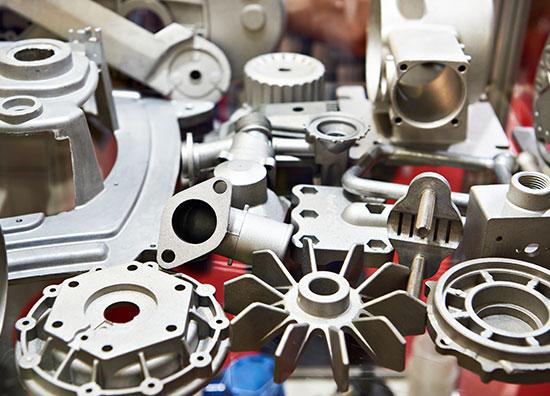
Aluminum Alloy Processing
Aluminum alloys are widely used in the automotive, motorcycle, and bicycle parts industries due to their lightweight, high strength, high ductility, excellent thermal conductivity, and ease of machining. These characteristics allow for extensive applications. Parts can be manufactured to meet specific appearance and dimensional requirements through processes such as aluminum forging, aluminum casting, gravity casting, or aluminum extrusion.
Metal Forging
Process :
Solid metal → Cutting → Pre-heating → Forging → Stamping → Heat treatment → Polishing → Tumbling → Sandblasting
Forging is a metal shaping process that involves applying pressure to a metal workpiece using forging machinery to acheive the desired shape. It allows the metal to attain specific mechanical properties, shape, and dimensions. Depending on the forging temperature, it can be classified as hot forging (above 800℃), warm forging (300℃~800℃), or cold forging (room temperature). Hot forging is the most commonly used technique in many industries.
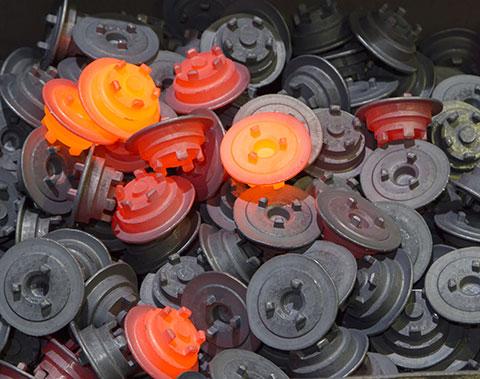
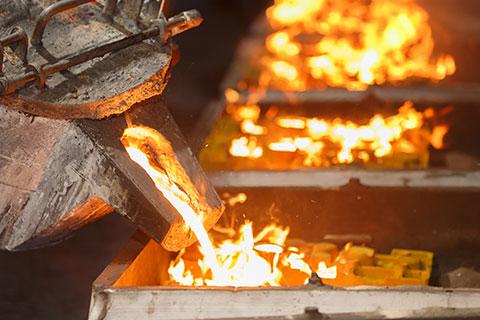
Metal Casting
Process : Molten metal → Molding → Solidifying and cooling → Cutting off → Grinding → Blasting → Heat treatment
Casting is a metal forming process where heated molten metal is poured into a mold to obtain the desired shape. It can be categorized into different casting types according to the mold and process used, such as gravity casting, die casting, low pressure casting, sand casting, lost wax casting, vacuum casting, continuous casting, etc.
Aluminum Extrusion
Process : Solid metal → Cutting → Pre-heating → Extrusion → Straightening → Cutting → Heat Treatment
Extrusion is a hot forming method in which a metal material is continuously passed through a die with a predetermined shape at extremely high pressure and temperature, by heating, plasticizing and screw extruding, and then cooled to form the desired shape. It is typically used to produce long or continuous shape parts such as rods, tubes, strips, etc. Commonly used extruded metal materials include aluminum, copper, magnesium, titanium, lead, etc., even brittle materials can also be extruded.
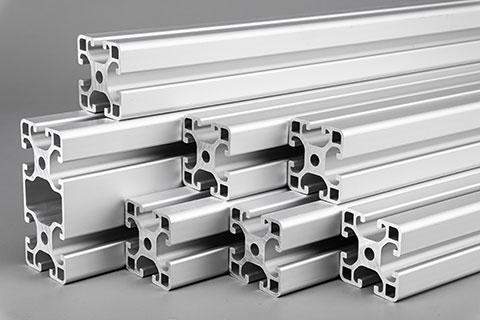
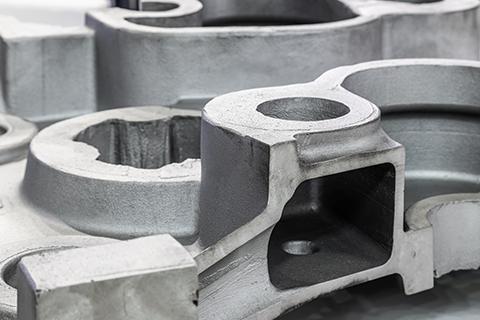
Powder Metallurgy
Process : Powder preparation → Mixing and blending → Compacting into mold → Sintering → Shaping → Heat treatment
Powder metallurgy is a manufacturing process that produces precision and highly accurate parts by pressing powdered metals and alloys into a rigid die under extreme pressure. The key process in powder metallurgy is sintering, which heats the parts to bond the powder particles. It is suitable for manufacturing high-precision, complex-shaped parts such as various aerospace parts, automotive parts and medical products. Materials used in metal powder metallurgy include iron, copper, aluminum, magnesium, titanium, chromium, nickel, cobalt, etc. Different materials can be mixed to produce different properties.