Powder Metallurgy
Process : Powder preparation → Mixing and blending → Compacting into mold → Sintering → Shaping → Heat treatment
Powder metallurgy is a manufacturing process that produces precision and highly accurate parts by pressing powdered metals and alloys into a rigid die under extreme pressure. The key process in powder metallurgy is sintering, which heats the parts to bond the powder particles. It is suitable for manufacturing high-precision, complex-shaped parts such as various aerospace parts, automotive parts and medical products. Materials used in metal powder metallurgy include iron, copper, aluminum, magnesium, titanium, chromium, nickel, cobalt, etc. Different materials can be mixed to produce different properties.
Advantages : Ability to produce complex-shaped parts, high precision, low cost, high material utilization, and reduce post-processing time.
Disadvantages : lower strength than forgings or castings, not suitable for small batch production.
Applicable industries : Automotive parts such as tire core, pulley, crankshaft, gears, etc.
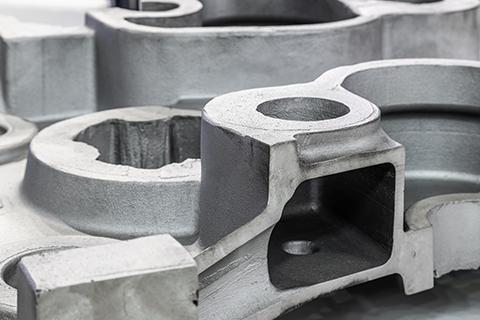